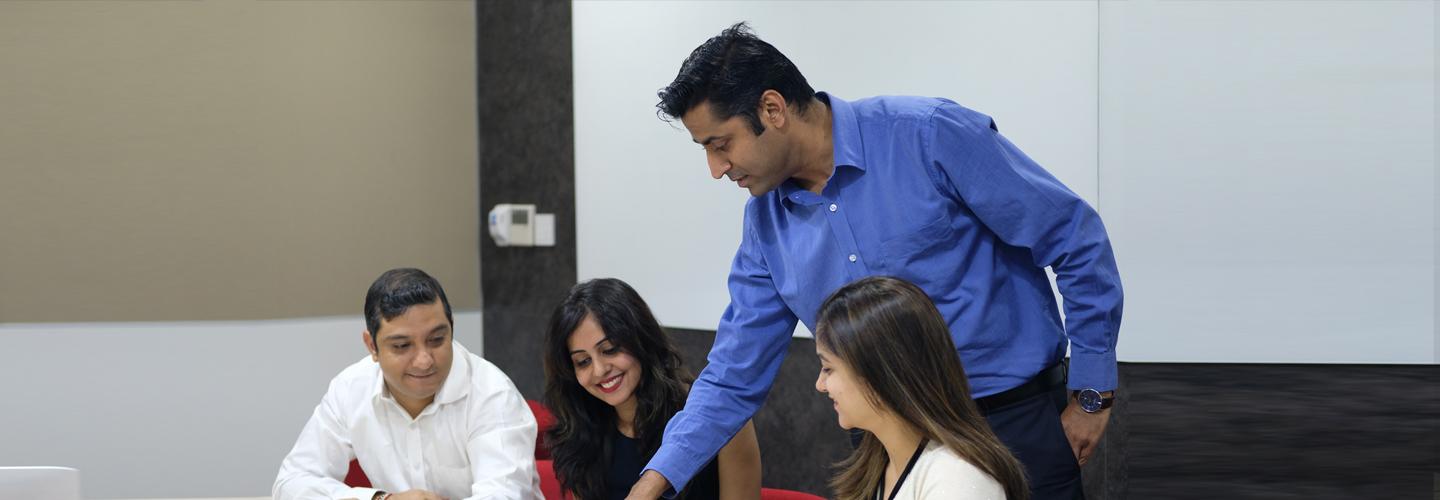
Improving our processes
An insight into the changes brought within the Plastics team to manage work effectively.
To make sure we safeguard our customers against fraud in an efficient manner, the Plastics team, on a daily basis investigates suspicious/fraudulent activity on debit cards.
To avoid fraud, the nature of the process calls for extreme caution while dealing with each case. The erstwhile process had the team working on nine queues, clearing the volumes on a daily basis and ensuring 100% compliance to quality.
As the process matured, it called for better utilisation of FTEs and generate bandwidth within the process to accommodate more work.
Improving process with customers in mind
Colleagues within the Plastics team introduced a robust in-house methodology with an effective and continuous monitoring of queues and training sessions aimed at bringing more efficiency, allowing our teams to service customers quicker and reduce dependency on onshore teams.
With Customer Service team previously handling a major portion of referral rate (cases/transactions referred to onshore team for additional investigation), training sessions were conducted for Plastics team members to monitor skillsets, and to gain a better understanding of the process and Customer Service team dependency.
Subsequently, the team was split into three groups as per their skillsets and work was distributed basis complexity. This approach led to improved accuracy and lower number of handoffs.
Subsequent trainings and calibration sessions led to improved processing time with teams achieving impressive efficiency rate. Spurred with the success through reduced referral rate, consistent quality and improved processing time, the Customer Service team transitioned additional queue to the Plastics team in January 2019.
Thus, optimum utilisation of workforce via cross-utilisation of resources in different areas of Fraud department created a strong workflow and contributed in making the team one-stop destination for all Fraud related activities.